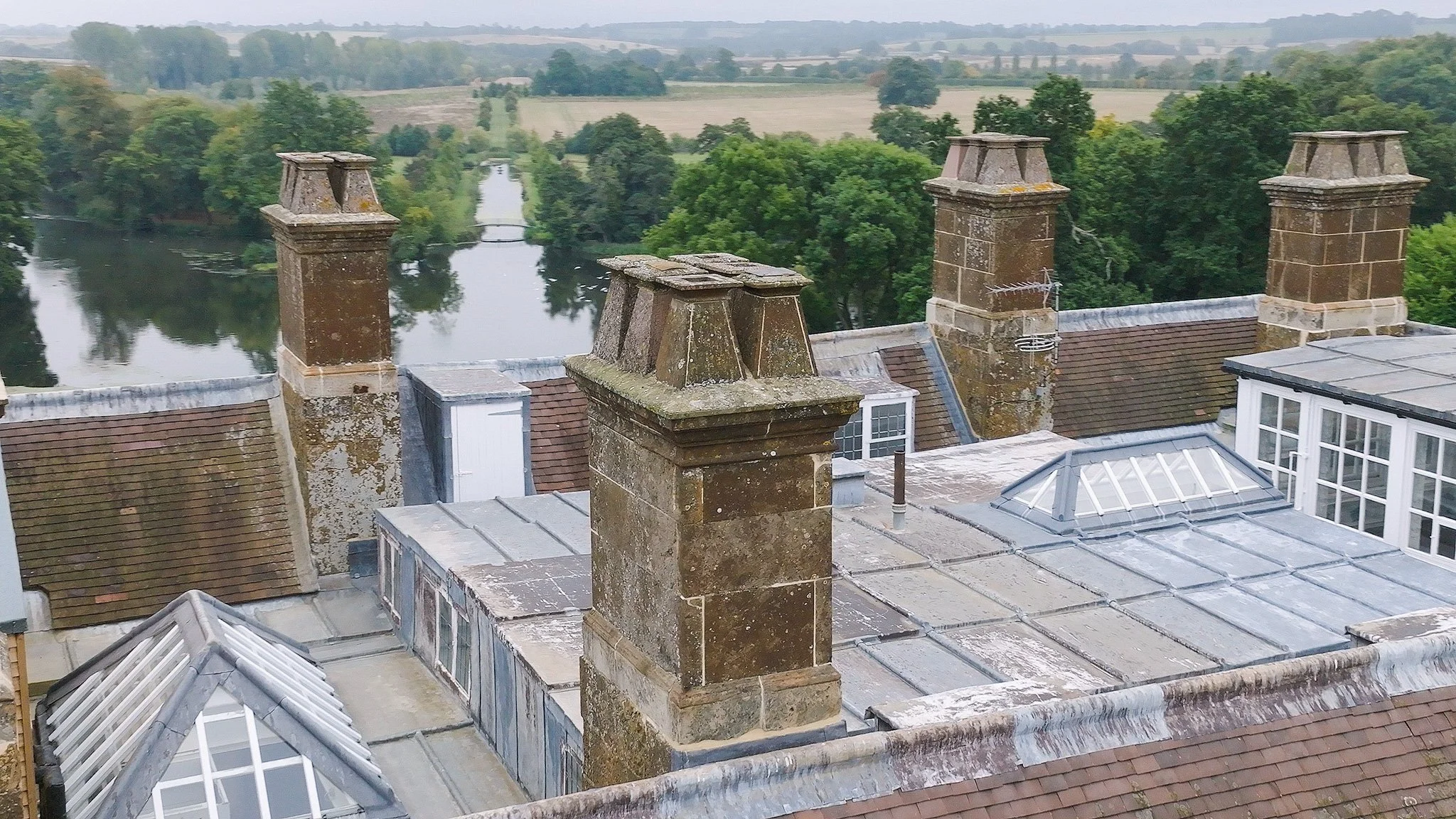
PRIVATE HOUSE, NORTHAMPTONSHIRE
Roof repairs to a Grade I listed 18th Century Country House – Northamptonshire.
© 2022 Cineflow aerial drone services
Good maintenance is fundamental to looking after any building, but a problem out of sight can be out of mind, which sometimes results in a significant repair bill when the issue is finally addressed. In 2019, we were commissioned to carry out a condition survey of a private house in Northamptonshire. The condition survey revealed that the roof required extensive work.
Much of the leadwork had failed due to fatigue as a result of exposure, and expansion and contraction. Our condition survey tracked leaks and damp in the attic rooms below attributable to defects in the roof finishes above – failure of these roof finishes was allowing water in and below the east pediment, causing the ceiling plaster to fail.
Given the quantity of repairs required alongside leadwork that did not comply with current guidance, our initial reaction was that the roof should be re-roofed. However, as a result of the requirement to install ventilation and improved drip details this would have involved alterations to the structure of the roof - potentially compromising significant historic fabric.
As a consequence, the project was undertaken as an extensive repair project - replacing defective leadwork that had split or failed. The repairs were estimated at £250,000 including contingencies in contrast to a cost of £600,000 for re-roofing.
Cracked lead to pediment causing damage to attic rooms internally
Split cover flashings
Lead work
The house was built between 1747 and 1750, it is rectangular in plan with a pitched tiled roof on all four sides with dormers hidden by parapets. Internally the roof has an inner flat roof approximately 1.5m higher than the external parapet gutter. The roof pitch on the inner roof has dormers and there is a raised lead roof to provide light to central attic rooms. The inner roof drains through four chute outlets - 2 on the north elevation and 2 on the west, which run through the roof void to the outer parapet and to downpipes on the north and south elevations. Netting was installed to stop the pigeons blocking the gutters.
Our heritage statement confirmed that use of the attics intensified in the 19th century. Graffiti on the side of the dormers confirmed leadwork dating from 1814. Huge lead bays survive on the raised section of the inner roof, dormer hoods and cheeks, and the raised section of roof to the inner roof.
The repair approach was to carry out repairs to defective lead sheets unless the extent of repairs made replacement necessary. A bespoke specification containing over 30 unique clauses and a photographic report were prepared to identify the defects and works required. Previous epoxy based polymer (plastic) and lead ‘patch’ repairs were identified, however, plastic repairs had cracked and failed so hot works were necessary to prolong the life of leadwork that had split. Lead sheets were identified for replacement where the lead was split through the rolls, or due to expansion and contraction. Sacrificial flashings were installed wherever possible.
Graffiti on dormers dating from 1814
Large lead bays
Lead bays
At either end of the pitched roof the house has two bays. These were originally covered in wider bays of 18th century lead formed with hollow rolled joints. Over the years the hollow rolls had become damaged due to loading deliveries on the roof. Listed building consent was received for changing the 3 bays on the north side of the roof and 6 on the south.
Replacement lead bays - with timber rolls
Lead pediments
The east pediment was in poor condition with several bays requiring replacement where they had rippled and failed. As mentioned previously the defects had caused the ceiling to fail. The plan was to replace the pediment with a new roof with timber core rolls, however, working with the roofing contractor we were able to modify the design of the roof to a hollow rolls roof to match more closely to the original roof. The existing fixing points were welded onto the edge of the parapet to repeat the historic detail.
Replacement pediment east (left) existing repaired west (right)
Vertical weathering
To the inside of the inner roof, the raised section had two extraordinarily long sections of lead weathering. The weathering was cracked to the south and west side of the roof. The damaged sections of weathering were removed and replaced with new lead in narrower bays welted to the historic leadwork. All the existing and new lead weathering was re-clipped to the dormer roof.
Weathering repairs
Dormer flashings
The abutment flashings to the dormers were unusual as they were constructed from a single sheet of lead that lapped over the tiling below. In one location the detail had been modified in the past - cutting away the overhanging flashing and exposing the soakers. As part of the works an extra lead flashing was installed so that the leadwork matched more closely the other dormer details.
Dormer and lead repairs
Lessons learnt
Despite concerns over the condition of the roof substrate below, very little timber repair was required. Contingencies had been allowed for repairs in the project but were never spent due to the existing penny gap boards and the limited amount of insulation within the roof.
Whilst the attic space is heated, and the roof insulated, no evidence of underside lead corrosion was reported. This further supported our decision not to install ventilation which would have involved re-roofing and inevitably increasing project risks such as structural repairs and the discovery of asbestos and ecological issues.
Conclusion
The repairs to the leadwork were extensive and mark the completion of a backlog of repairs. Over the next few years, the repairs will allow the condition of the attic rooms to stabilise and dry out. Significant future works have been prevented and will be avoided through regular condition inspections so that repairs are incorporated into planned maintenance such as gutter clearing and decoration.
The repair project provided the opportunity to address poorly executed previous works, e.g. replacing felt soakers with lead. Thanks to some careful installation of discreet stainless-steel mesh the intrusive pigeon netting was also removed. All new work was carried out using traditional materials and techniques including lead welding repairs using lead of a compatible thickness to ensure that repairs were long lasting and did not fail in the future.
The project was delivered on time and budget at £175,000 and took 28 weeks.
The new repairs are currently obvious but in the fullness of time will dull down to match the existing leadwork. Owing to the repairs approach, the alterations will always be noticeable to the trained eye. The achievement of this project is that the roof is now water tight, and that the significance of the roof design and historic leadwork is preserved for the future.
Roof repairs to Grade I listed Country House, Northamptonshire
Project team:
Client – Private
Rural Property Consultancy Ltd. – Mark Juniper
Estate Office – Hamish Gairdner and Jane Margieson
James Mackintosh Architects – James Mackintosh
Lang Conservation – Geoff Beetham and Neil Nightingale
Construction period 6months.
Construction cost/sqm: £250 ex VAT